随着汽车工业化的不断发展,无论从经济上还是性能上,对汽车材料的要求是越来越高,由于铝合金有减重、节能和更好的回收再生性,汽车用铝合金材料会带来巨大的经济效益和社会效益。随着汽车节能减排及安全性要求的不断提高,汽车的结构件、底盘产品、车身连接支架、发动机部件等越来越多的产品都采用铝合金成型的零件,并采用先进的装配技术或先进的装配工艺进行装配,如下图示汽车前轮支撑骨架,是通过连接一个减震支架,实现汽车在行驶过程中的减震功能。减震支架由3部分构成:减震支架本体,橡胶支撑块,盖子,然后通过旋铆工艺将减震支架本体,橡胶支撑块,盖子装配在一起,形成减震支架总成产品,最后通过螺钉固定在车身的连接支撑柱上,实现汽车在行驶过程中的减震功能,满足汽车在行驶过程中的舒适性。在本文中,主要通过产品整个生产过程的工艺设计,实现产品最终旋铆装配工艺要求。
1产品技术要求
1)由于该产品在每一辆汽车上需要用到4个产品,产能要求高。
2)尺寸要求稳定、合格。
3)需要在340度的高温下保温4小时。
4)旋铆处不能有裂纹,疲劳试验满足要求。从技术要求上看,所有的工艺设计都要满足最终的旋铆工序。所谓旋铆,就是使用旋转设备,在外力的作用下,使用铝合金材料按照规定的形状进行延展,形成一个连接的永久塑性变形的装配过程。影响旋铆工艺的参数也是非常多的,如产品内部残余应力,产品尺寸,产品内部质量等等。这就要求我们在生产的各个工艺环节确保产品符合性。这里重点介绍如何设计产品实现的工艺过程,满足产品最终的旋铆工艺要求。
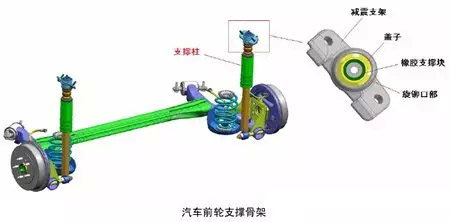
时效处理是为了消除零件内部的残余应力,稳定零件的内部组织和尺寸,改善零件的机械性能。通过对零件的时效处理,可以使零件内部的应力释放或相互抵消,以免在加工过程中零部件存在应力失衡而导致零件加工报废。如何解决在340度的高温时效处理产生的缺陷是我们首要解决的问题:
按照传统压铸的工艺,在压铸过程中,我们不可能避免遇到产品内部的气孔缺陷。主要有以下原因:
A.模具型腔本来就是一个含有空气的空间。
B.由于浇注设计的不合理造成卷气。
C.铝合金在由固体溶化成液体时,铝在液态下与水气发生下列反应:
2Al(液)+3H2O(气)=γ(Al2O3(固))+6[H](溶于铝液中)
产生的气体可能在压铸过程中就会造成产品气孔缺陷,当含有气体的产品在340度的高温下保温4个小时,那么产品内部的气体就会释放出来,在产品表面形成一个一个的气泡(如图),无法满足的产品的质量要求。通过以上的种种原因分析,虽然我们无法将所有产生产气孔的消除,但是我们可以将它控制的可接受的范围之内,以满足客户的要求。
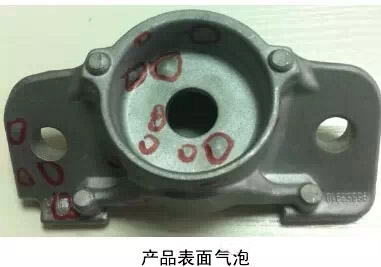
2模具设计、模拟
我们采用的1模6件的多型腔结构,满足客户的产能要求,并且通过模拟分析软件进行压铸过程模拟分析,确保浇注系统的内角口同时进水,避免多股支浇道不同步进入型腔,造成卷气而形成气孔。
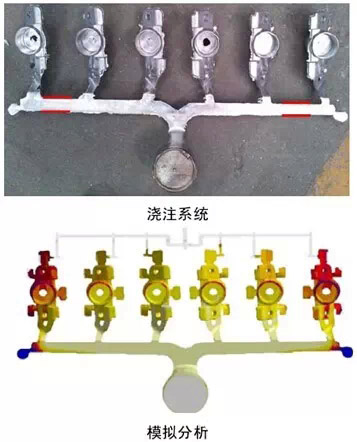
3抽真空工艺的运用
为了确保模具整个型腔内在生产过程处于一个相对真空的状态,我们引进瑞士FONDAREX抽真空系统及相关的抽真空工艺,通过抽真空的方式能够实现在铝合金液体在进入模具型腔内是一个相对真空的空间,那么铝合金液体在这样一个相对真空的空间内成型,无法接触到空气中的气体,大大减少了卷入气体的可能性,提高了产品的内部质量。一般我们用真空度这个参数来衡量这个相对密封的空间,并且进行生产过程的过程控制。
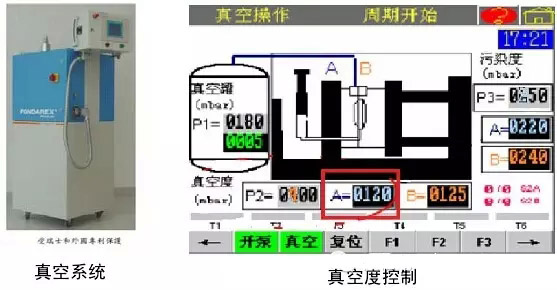
4铝合金液体除气工艺及含氢量检测
1)除气是把惰性气体喷入熔融铝液以达到去除氢气的目的。我们采用的是旋转式除气,是通过高速旋转并喷射惰性气体的转子把惰性气体大气泡打散成非常细微的小气泡,并使其均匀地分散在金属液中,使得更多的惰性气泡表面和金属液中的氢气和杂质接触从而把这些有害物质带到液体表面,从而减少液体中的气体。
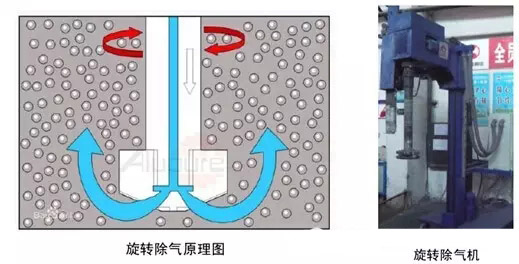
2)液体除气完成后,需要对液体的含氢量进行检测,确保含氢量在工艺可控的范围。首先在铝液心部取70%-80%的铝水将装铝水的坩埚在20s内放入真空室内,迅速盖上盖子。180s后取出样块,进行对比判定。在真空的情况下,如果铝液里含有气体,那么样品上就会鼓起气泡,含气量越多鼓起的气泡越大,通过对比的方式来保证铝液的符合性。
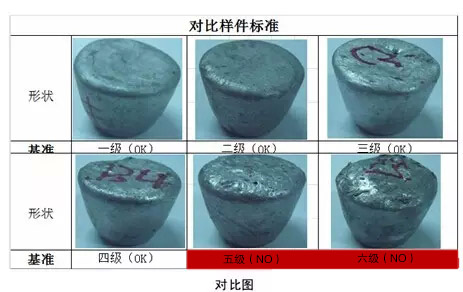
5产品的时效处理
铝合金保温温度、保温时间、冷却时间按以下方式:

工艺要求:
1)先将炉子升温到340度(产品可随炉升温),必须340度下保温4小时。
2)对产品进行色彩标识,能够识别是否已经进行了时效处理。
3)零件应该装在专用框中,保持一定的间距,保证空气的流动。
4)对时效的温度实时监控,每班对时效炉的温度曲线进行检查。
检验与验收:
1)检查色彩标识,色彩随着温度变化而变化,观察颜色温度达到340度。
2)对产品硬度检测,硬度要求:50<硬度<70HB。
3)产品表面的气泡。
6结论
通过以上工艺过程的设计及控制,我们基本上满足了产品在旋铆过程的稳定性,实现了采用先进的装配工艺进行装配的工艺。如果在生产过程中出现旋铆裂纹,我们可以通过以下2种情况进行分析原因和解决问题:
1)正常出现裂纹(图1),形状为非常规则的裂纹,这个产生的原因主要旋铆过程工艺的不稳定性,需要对旋铆工艺参数进行细微的调整。
2)异常出现裂纹(图2),形状为齿形的裂纹,这个产生的原因主要是产品本身在生产过程出现了异常,如材料、真空机、时效、过程参数等,需要我们针对具体的问题进行逐一分析解决。
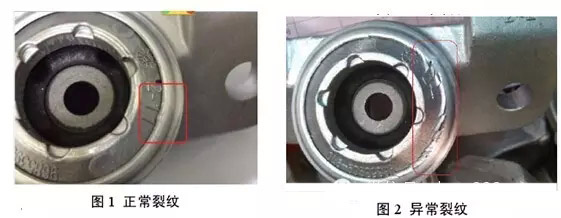
PS:易模网模具及压铸件专题采购对接会(2015年4月28日)正在火热报名中!
详情请登录 www.cmpc.cc 了解该活动或关注微信号cmpc-cc→采配会→采配会预告(或采配会报名)
|