250km动车组轴箱体是转向架的重要部件,其与轴承装置是联系构架和轮对的活动关节,使轮对的滚动转化为车体沿钢轨的平动,在承受列车重量的同时传递各方向的作用力。
200km动车组轴箱体开始阶段从日本川崎进口,为进一步使200km动车组国产化,2013年公司开始开发研制250km统型轴箱体。
轴箱体属于重要部件,其加工精度要求高,通过对加工试制过程的跟踪分析,合理利用柔性生产线加工轴箱体,解决加工过程中的质量问题,制定切实可行的加工工艺方案,既能保证轴箱体的加工精度符合设计要求,又能提高轴箱体的加工能力与质量,质量与效率得到很大提升,满足了生产需要。
1.加工设备:
轴箱体柔性加工生产线由信息系统、加工系统和物料输送系统组成(见图1)。
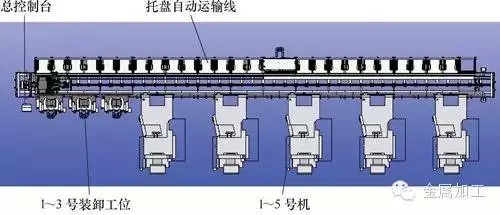
图1
信息系统是生产线的总控制台,主要进行加工程序编辑、作业管理、刀具管理等。
加工系统由5台NH63000DCGII主机设备组成。5台设备分别按照1号机、2号机、3号机、4号机及5号机依次布置,在1号机带有U轴刀具。每台设备的刀具容量为100把,具有在线检测、刀具破损检测等功能。
物料输送系统由上、下两层托盘架共48个托盘位、3个装卸工位及1条托盘自动运输线组成。轴箱体生产线根据生产需求,配备了32个安装工件工装的托盘。物料输送系统根据总控制台的作业安排将托盘送至托盘位、装卸工位及5台设备待加工位。
2.加工特点:
轴箱体加工特点为:①轴箱体通过一、二工位两次装夹,完成全部尺寸加工。②根据生产要求,可进行多个产品并行生产加工。③轴箱体生产线在各工序加工刀具满足使用要求的情况下,可实现连续工作、无人自动作业。④在设定好加工计划后,针对临时加急生产计划,在总控制台进行计划优先调整,可方便应对生产突发状况。
3.产品情况:
产品材质为ZG25MnNi,属于铸造件,轴箱体抗冲击性能、拉伸及延展性等力学性能高,但存在砂眼、硬点、夹砂及焊修硬点等铸造缺陷,此类缺陷易损坏刀具,降低刀片的耐用度,影响工件加工精度。
4.工艺特点:
根据公司配套经济化要求,轴箱体外供来料毛坯粗加工后,单边留量1.0~1.5mm,在轴箱体柔性加工生产线上加工时,根据工装设计需要,部分粗加工留量定为工艺定位尺寸,规定了配合公差。
5.加工过程:
所要加工的轴箱体如图2所示。采用两工位装夹,完成全部尺寸加工要求。
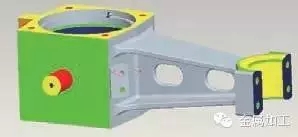
(1)一工位平装。轴箱体平放,使用来料粗加工后的内孔,利用一面两销定位夹紧方式(见图3),加工完成弹簧圆柱及底面、清障面、轴温检测器、时时轴温传感器安装座各部尺寸、减振器座、注油孔各部尺寸,并钻攻此工位各部螺纹孔。
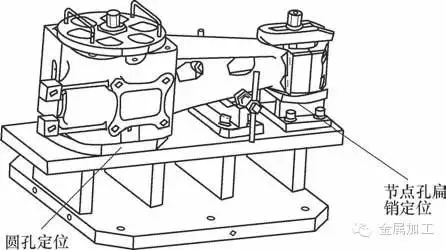
(2)二工位立装。采用弹簧面的50mm圆柱及底平面与节点端得活动定位来装夹工件(见图4)。加工完成轴承孔孔径及两端面、节点孔及两端面各部尺寸、钻注油孔内侧倒角,并钻攻此工位各部螺纹孔。
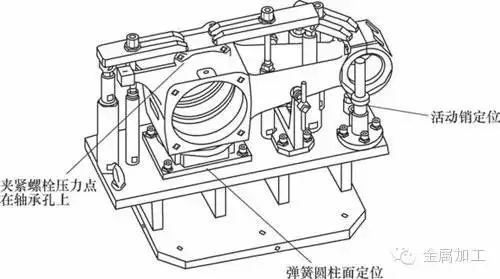
6.加工工艺难点:
(1)时时轴温传感器安装座加工:为保证高速动车组行车安全,随时检测轴箱轴承装置在运行过程中的温度变化,避免轴箱轴承装置温度过高而造成行车安全隐患,250km动车组轴箱体在200km动车组轴箱体的基础上增加了时时轴温传感器装置,设计了时时轴温传感器安装座。
时时轴温传感器安装座与轴箱体轴承孔与节点孔中心线夹角为35°,安装座2个M16-6H螺纹孔深48mm,螺纹有效长度43mm,与之配合的传感器螺栓精度为6g,配合间隙小于0.02mm(见图5)。因中心夹角为35°,造成加工空间较窄,数控设备加工过程中主轴与节点孔外壁产生干涉,因此需采用加长刀具解决。但刀具加长,铣面过程中刀具振动,加工面表面粗糙度值超差。螺纹旋合长度大,较难保证配合精度,面铣刀、丝锥刀体的选用为此工序的难点。
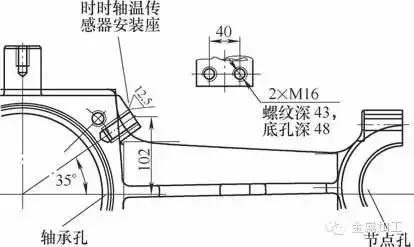
(2)轴承孔各部加工:轴承的孔端面以及孔内各尺寸(φ235+0.046+0mm、φ230+0.044+0.015mm)、形状和位置精度要求高,圆度0.02mm,圆柱度0.02mm,垂直度0.02mm,节点端面对轴承端面垂直度0.05mm,节点孔对端面垂直度0.05mm。轴承孔的设计尺寸要求如图6所示。
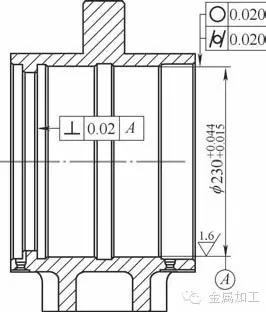
要满足轴箱体的加工精度要求,既需要先进的加工设备、合理的工装,又要由正确的工艺方法保证。在满足各项加工要求的情况下,同时要兼顾生产效率、保证生产进度,满足生产需求。
7.安装座加工工艺分析及问题的解决:
时时轴温传感器安装座加工工艺为:铣安装面→钻螺纹孔底孔→倒角→攻2个M16-6H螺纹孔。加工过程中,因主轴和轴箱体易产生干涉,通过刀具选用及编辑程序时使用合理的切削参数来解决。
(1)铣安装面:选用φ63mm加长面铣刀粗精加工,φ63mm面铣刀半径小,可提高主轴转速,减少每齿进给量,降低刀具振动,提高减振器表面质量。
(2)钻螺纹孔底孔:因使用加长夹持钻头刀杆,钻孔过程中易造成底孔偏大,钻孔攻螺纹后,虽塞规检测合格,但螺纹孔中径超差,出现产品质量问题,导致工件报废,因此螺纹孔底孔采用φ13.8mm内冷钻头啄钻钻孔指令加工。φ13.8mm钻头直径稍小于螺纹孔中径要求,可以避免中径超差问题;内冷方式切削液充分冷却,降低钻头磨耗;啄钻钻孔指令G83及时排屑,防止切屑缠绕造成孔径超差,Q参数变化可控制钻屑大小及加工效率。
(3)倒角:此加工程序中应用了破损检测指令M103,破损检测指令作用是检测钻头的长度,防止因钻头破损,钻孔深度无法满足攻螺纹要求而造成质量问题。
(4)攻螺纹:采用刚性夹头夹紧丝锥,中间增加弹性夹套。
此方法避免了攻螺纹过程中因异常情况造成螺纹孔质量问题,提高了螺纹孔的加工精度。
通过分析研究,选用合理的刀具、编辑正确程序及使用合理的切削参数,解决了时时轴温传感器安装座加工过程中出现的问题,满足了该部位全部尺寸的加工设计要求。
8.轴承孔加工工艺分析及改进:
此工位将一工位加工的弹簧圆柱及底面为定位销、面,节点面活动销定位,而工件定位夹紧后,需将活动定位销取走,此定位方式能保证完全定位(见图3)。
(1)原因分析。轴承孔加工后检测尺寸合格,加工全部尺寸后,送三坐标检测轴承孔,发现孔尺寸、圆度和圆柱度超差。分析其主要原因为:①轴承孔外壁形状不相同,切削参数不合理造成。②装夹方式错误造成。
(2)工艺改进。通过选用TCGT110208EL、TCGT110204EL、TCMT090204-24、TCMT110208-PF4、TCGT110208EL带涂层和TCMT110208-24共6种精镗刀片,转速n=200~300r/min,进给量f=0.14~0.20mm/r,背吃刀量ap=0.14~0.20mm(直径方向0.28~0.40mm)。经验证,发现TCMT110208-24刀具结构设计合理,硬度较高,该刀片使用切削参数为:转速n=250r/min,进给量f=0.16mm/r,背吃刀量ap=0.15mm。1个刀片角可以加工达到尺寸、表面粗糙度值要求的5个轴箱体,但加工后去除夹紧力,轴箱体内孔仍然变形。
进一步分析装夹方式,发现加工采用压板压紧轴承孔外侧,加工后去除夹紧力,轴箱体内孔变形,因此其装夹定位方式存在不合理性,造成轴承孔尺寸、圆度和圆柱度超差。
重新改进二工位装夹定位方式(见图7),利用工件减震器安装孔短销定位,清障面4×M20螺纹孔夹紧,增加轴箱小端工艺定位面。采用此定位装夹方式,轴箱体轴承孔无压紧力,加工后无变形现象,加工尺寸满足设计要求。
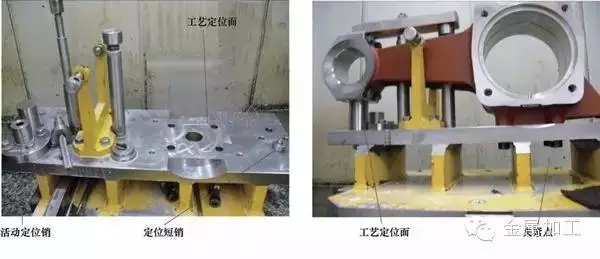
图7 改进后的二工位装夹定位示意图
9.止推面加工工艺分析及改进:
轴承止推面与轴承孔中心线垂直度为0.02mm,常规加工方法是选用同一把三面刃铣刀(见图8a)分两刀粗、精加工完成。三面刃铣刀刀片材质为WKP35,属镀层硬质合金类材质,刀片型号为LNMU100508-F57T,根据ISO1832-2004切削刀具用可转位刀片——名称与符号,分析三面刃铣刀刀片参数(见附表),三面刃铣刀刀片呈正方形,无后角和主偏角,刀片偏差大,属于粗加工类刀具,因此无法有效地满足止推面的加工要求。
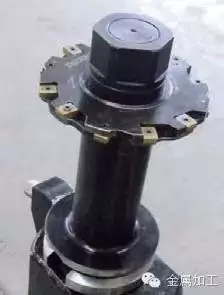
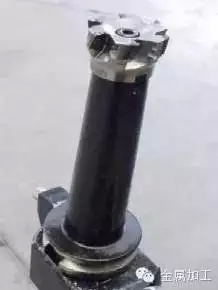

而三面刃铣刀分粗、精加工时,还有以下缺点:
(1)深度加工尺寸基准不统一。三面刃铣刀刀杆有效长度为150mm,只能从轴箱盖侧加工轴承孔深度,与轴承孔深度198-0-0.2mm基准不统一,对于工件坐标系的建立,相关刀具长度补偿等要求非常精密,不允许存在误差。
(2)加工效率低。铣刀直径为φ125mm,根据公式计算进给量为160mm/min。
(3)刀片利用率低。精加工时只有一侧刃参与切削,刀片寿命低,为满足垂直度及表面粗糙度要求,需及时更换刀片,容易造成浪费。
(4)辅助时间长。为保证更换后的刀片在同一平面内,需要大量时间更换刀片。
由于三面刃铣刀存在缺点,为满足轴承止推面加工精度要求,需要重新进行刀具设计。根据加工要求及刀具加工原理,设计选用φ50mm面铣刀(见图8b),刀杆有效长度为250mm。刀片材质为WKP25,属镀层硬质合金。刀片型号为ADKT10T3PER-F56,分析面铣刀刀片参数,面铣刀刀片呈棱形,15°后角、90°主偏角,刀片偏差小,排屑好,切削和夹紧特征合理,是快换精加工刀片,可满足止推面加工要求。
面铣刀具有以下优点:
一是深度加工尺寸基准统一。面铣刀从轴承侧加工轴承孔深度,因此基准统一。
二是加工效率高。铣刀直径为φ50mm,根据切削参数公式计算进给量为400mm/min。
三是刀片角度参数合理。刀片利用率高,加工性能高。
四是辅助时间短。因选用快换刀片,更换刀片时间可忽略不计。
工艺改进后,三坐标检测主要形位公差数据如图9所示。数据表明,新工艺保证了产品的质量要求。
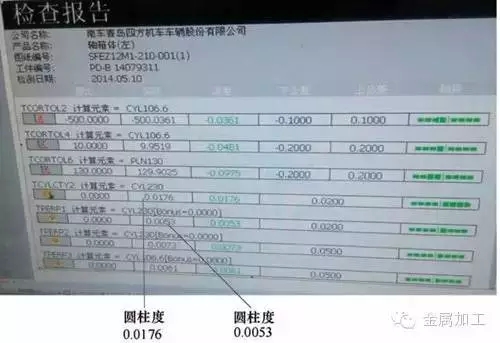
10.结语:
在后期的轴箱体批量生产中,改进后的装夹定位及新刀具使用满足了产品的加工质量要求,同时提高了生产效率,进一步提高了转向架的制造水平,同时为轴箱体装夹定位及深槽端面加工积累了经验。
来源:《金属加工(冷加工)》2015年第12期,作者单位:南车青岛四方机车车辆股份有限公司
|