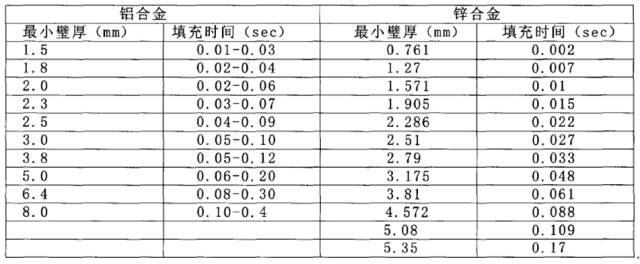
如果按照此表来,那么我们的流量法就简直就没法用了。这里我简单的接地气的用2个方法来告诉大家简单的方法。
(G件+G排)/2.5*0.05*40
2.5当然是铝液的密度,制件和渣包重量以克为单位。这里我们要注意,此时在填充状态,密度应该按照液态密度计算。此公式适合铝合金在3-6毫米壁厚使用,我们所接触的合金件往往大都在这个范围之内。因为流量过大往往产品出现含气量增多,虽然工艺上更能满足高速高压的工艺,但是一旦时间过短,造成型腔内气体没有充足时间排除,那么产品含气量必然增多。如果填充时间多长,那么我们经常看到产品冷隔,发黑,疏松甚至开模时产品开裂等一些列的问题。所以无论从外观件还是气密件来讲,产品的填充时间是尤为重要的。第二个方法基本可以制定产品重量的27%-30%来计算产品需要的内浇口截面积,厚壁件取前者,薄壁件取后者,以3毫米为界分。以这2种方式来确定内浇口范围,略微的差距我们可以在压铸机上做微调。这里只是简单的讲诉一下内浇口实用的计算和判断的方法,没有详细讲解模具材料系数,液固相的范围,如果要详细解答来龙去脉,相信需要写一本书,不合适我们压铸人现场处理的方法。
2、流向问题:如果说内浇口截面积是满足流量的话,那么浇口就是来确定合金液的流向,往后延伸流道也是来满足合金液的流向。浇口指的是内浇口和流道之间的过度区域,一般分为扇形浇口和锥形浇口,关于浇口的面积计算我们以后有时间可以专门来详细的讲解,这里我们主要讲一下方向位置问题。其实流向也是至关重要的问题,一般我们根据产品来确定浇口位置,那么问题来了,一般直接和浇口连接的制件基本成型外观包括密度都比较理想,而位置较远的相对较差。这里主要关系到的是主填充区和非填充区,一般主填充区是浇口附近或是方向一致的区域,非主填充区我们称之为挤压区。如果产品位置充足,最佳的是让主填充区占据产品的2/3。(这里的2/3是指产品流经区域,并非指内浇口面积)。当然每个制件不一样,这需要我们更加精准的去判断。这里主要讲几点方法:
(1)在正常情况下,尽量使产品同步进料。
(2)尽量保持较多的直接填充区域。
(3)根据制件的要求分别选择浇口的位置,致密件按照逐层凝固或者顺 序凝固的方法,以尽量减少产品的缩孔,尽可能的打散产品内的气孔,以能达到产品的补缩问题。如图:
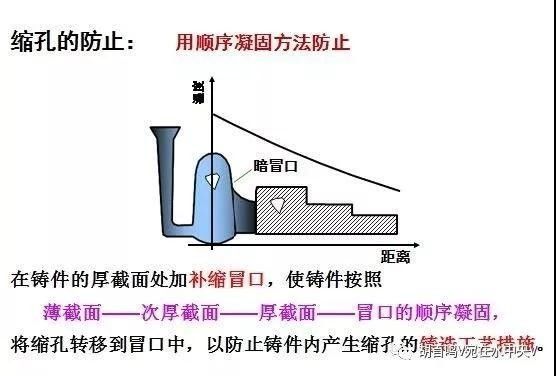
当然在有些产品我们需要格外注意,那就是厚度变化较大较多,起伏不稳定,变化起伏达到4倍或者更高的时候就不能一味的去考虑以浇口补缩的方式了,因为这些区域任你在怎么补缩都是无济于事了,那就需要考虑别的方法,比如料温的控制,冷却模温的控制或者流向的先后差异与料温冷热偶合的控制,或者加局部增压,有甚者更是考虑压铸模锻半固态等工艺。后者就比较难了,已经超出我们对产品前期的预判,需要借助模拟等手段来判断了。所以在开发产品时候最佳的是壁厚均匀,厚度差尽量控制在2倍以内,减少产品的2次爆发的区域。产品的厚度一般在4毫米左右,抗拉强度塑形变形等达到最佳,亦不易产生缩孔。随着产品的厚度增加其抗拉强度会逐渐减少。
(4)根据制件的要求分别选择浇口的位置,外观件按照同步凝固的方式的方法,以尽量减少产品的变形,或者以变形应力等引起的冷裂拉伤等缺陷。如图:
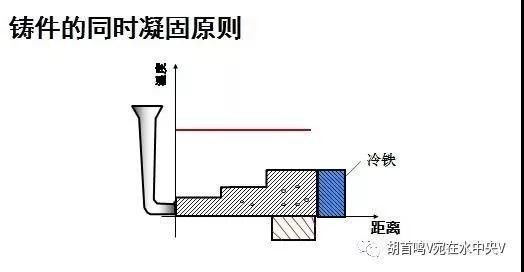
(5)尽量避免冲击产品的阻碍区域,流向要稳定,尽可能的保持原来浇口给的流向,一般合金液体在受到型腔的撞击后流向都会改变,如果连续过多撞击会造成合金液的死流,死流是我们压铸和模具设计最大的忌讳,合金液一旦流动不连续或者撞击后没有足够能量来驱使流动,那么气缩孔包括对接冷隔,冷料等一些列的缺陷就更容易产生。产品内的形状我们是没法控制的,但是尽可能的去避免我们是能做到的。一味的撞击阻碍区域除了流向改变,还会使模具产生冲蚀,麻点,早期龟裂等破坏模具的现象。
(6)产品的流程尽量控制在流程和壁厚比的100-150之间。薄壁件取前者,厚壁件取后者。
(7)在产品浇口面积充足又形状变化不大的情况下尽可能的减少浇口的数量,如果是扇形浇口那么单路浇口的宽度不要超过80mm,角度小于90度。尽量别冲击制件排气区域,这个道理很简单,一旦排气封死,那么制件内部还在流动的话那么产品都是缺陷了。